In this month’s blog post, I will provide an overview of the similarities, differences, and advantages between particulate and coalescing air filters, with a focus on systems that include refrigerated air dryers and/or desiccant air dryers, referencing products offered within Altec AIR's A Series and A-PRO Series lines of Compressed Air Filters.
Similarities between Particulate and Coalescing Air Filters:
- Purpose: Both particulate and coalescing filters are designed to remove contaminants from compressed air systems, ensuring clean and dry air for various applications.
- Filtration Mechanism: They both use specialized filter media to trap and retain particles, but coalescing filters have an additional mechanism to remove liquid aerosols from the compressed air.
Differences between Particulate and Coalescing Air Filters:
- Filtration Level: Particulate filters primarily remove solid particles, while coalescing filters go a step further and remove liquid aerosols, such as oil and water, in addition to solid particles.
- Application: Particulate filters are often used as pre-filters to protect downstream equipment and air tools, while coalescing filters are utilized as secondary filtration stages or primary filters in critical applications requiring higher air quality.
Advantages of Particulate and Coalescing Air Filters:
- Particulate Filters: They are cost-effective and provide a basic level of filtration, suitable for general industrial applications where only solid particle removal is necessary.
- Coalescing Filters: These filters offer higher air quality by effectively removing liquid aerosols, making them crucial for sensitive industries like pharmaceuticals, electronics, and food processing..
Available Filter Element Classes:
X5 | X1 | XA | AC | |
Particle Removal | 5 micron | 1 micron | 0.01 micron | 0.01 micron |
Maximum Particle Size Class | 4 | 3 | 1 | 1 |
Maximum Oil Content | 4 | 3 | 1 | 1 |
Maximum Oil Carryover (at 68°F / 20°C) |
5 ppm / 5 mg/m3 |
0.3 ppm / 0.3 mg/m3 |
0.01 ppm / 0.1 mg/m3 |
0.003 ppm / 0.003 mg/m3 |
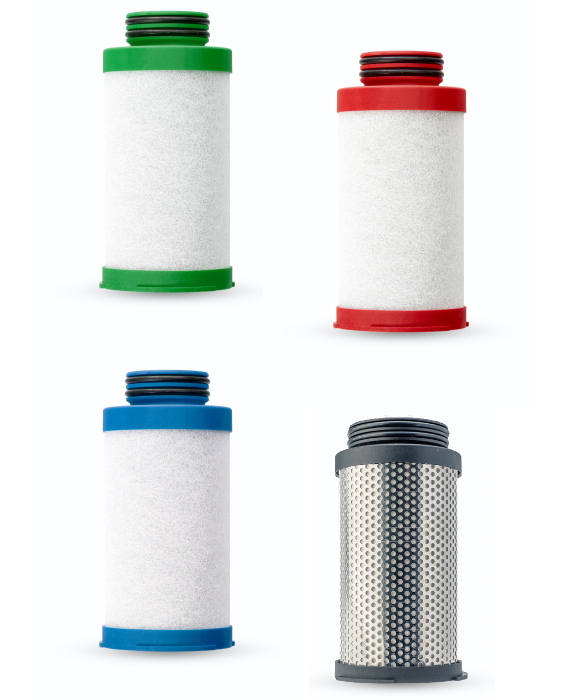
Usage in Systems with Refrigerated Air Dryers:
Refrigerated air dryers are commonly used for general industrial applications where a dew point of around 35-40°F is sufficient. In such systems:
- Particulate filters are installed as pre-filters to remove solid particles before the compressed air enters the air dryer, protecting the dryer's internal components and improving its efficiency.
- Coalescing filters can be installed as pre-filters in order to serve as protection to the air dryer, as well as placed after the refrigerated air dryer to remove any remaining liquid aerosols and solid particles, ensuring the delivery of clean, dry air to downstream equipment.
Usage in Systems with Desiccant Air Dryers:
Desiccant air dryers are employed in applications where a lower dew point, typically -40°F or lower, is required, such as critical manufacturing processes and sensitive instrumentation. In these systems:
- Particulate filters serve as pre-filters before the air enters the air dryer, preventing any larger particles from damaging the dryer and the desiccant material.
- Coalescing filters can again be used as pre-filters in order to protect the air dryer. Additionally, they may be installed after the desiccant air dryer to ensure the removal of any remaining liquid aerosols and solid particles. They play a crucial role in maintaining the high air quality required for these critical applications.
Clogging and Replacement:
Both particulate and coalescing filters can become clogged or dirty over time due to the accumulation of particles and contaminants. When filters get clogged, the pressure drop across them increases, reducing the efficiency of the compressed air system and possibly leading to equipment damage or performance issues. Regular inspection of the filter elements is essential to identify any signs of clogging or degradation.
Timely replacement of filter elements is crucial to ensure that the filters continue to operate effectively. Filter replacement intervals will be based on operating conditions, including compressor type, ambient & inlet temperatures, relative humidity, and more. In addition, filter inspection and replacement may be crucial in order to meet any downstream air quality requirements. By creating and adhering to a filter replacement schedule and conducting routine inspections, service technicians can help maintain the compressed air system's efficiency, protect downstream equipment, and ensure the desired air quality for various applications.
For more information on Altec AIR’s full line of Compressed Air Filters, visit: